Making functional, curved piezoceramics in a controllable manner
Functional piezoceramics can be used in sensors and actuators, yet brittleness of the material and its difficulty in shaping after fabrication have hindered its applications. A research led by a scientist from City University of Hong Kong (CityU) has proposed a pioneering and simple fabrication method that combined heat and gravity, to produce functional, curved piezoceramics in a controllable manner. Their findings enabled researchers to develop functional piezoceramics in different curved shapes according to the applications, which could accelerate the development of functional ceramic-based robotics, electronics and semiconductors.
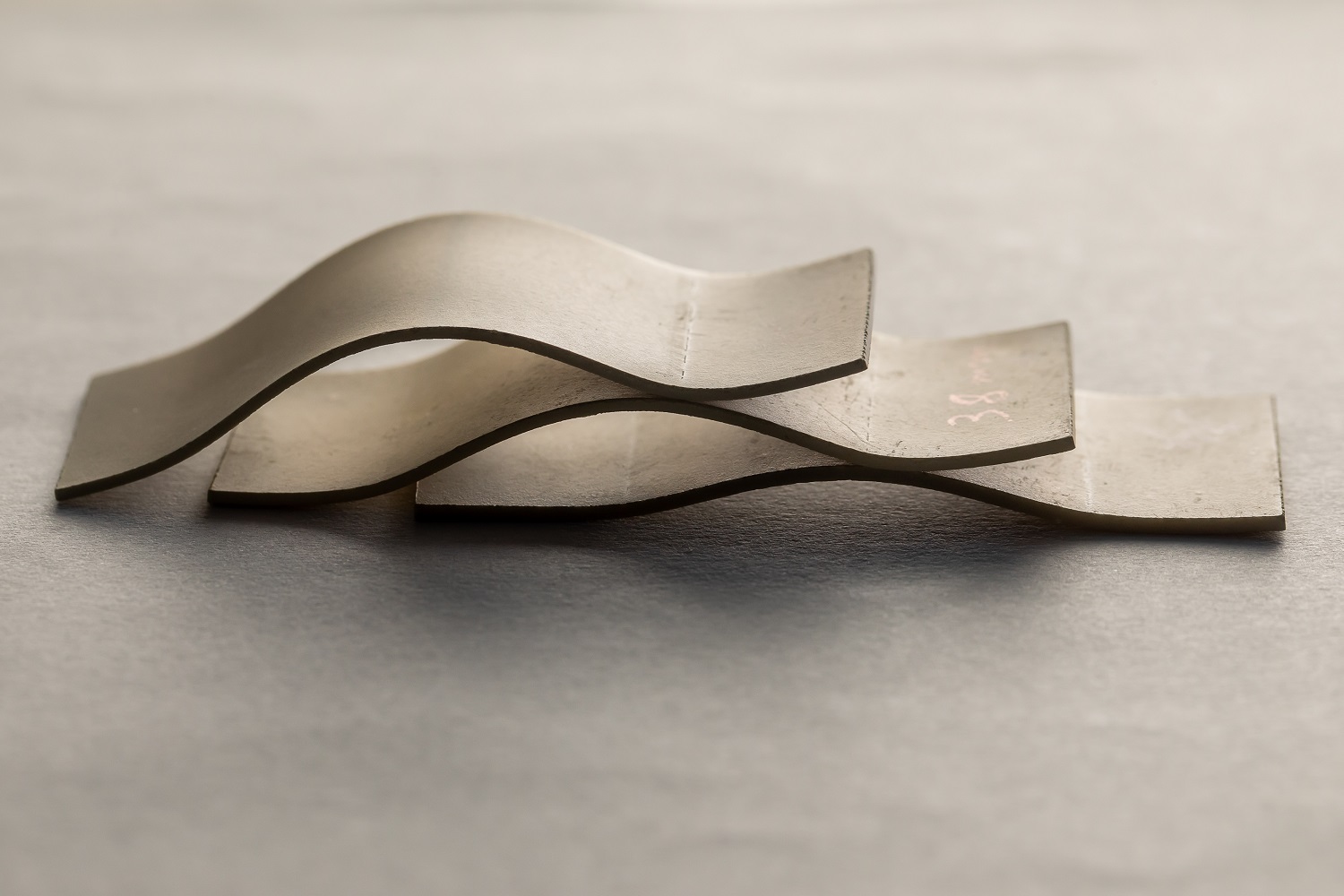
The research team was led by Dr Yang Zhengbao, Assistant Professor in the Department of Mechanical Engineering (MNE) . Their paper was published in the scientific journal Nature Communications, titled “A gravity-driven sintering method to fabricate geometrically complex compact piezoceramics”.
Problem of shaping functional piezoceramics solved
Piezoceramics, a typical type of functional ceramics, have been widely used in electronic and energy devices, thanks to their stable mechanical properties and low cost.
3D printing is commonly used in the industry to produce piezoceramics components in different shapes. However, due to technology limitations, it is not easy to “print” curved, compact ceramics. And there is always a trade-off between the shape and the piezoelectric performance. Piezoelectricity means electricity resulting from pressure, known as the piezoelectric effect.
To deal with the technology bottleneck, Dr Yang’s team skillfully took advantage of gravity in the sintering process and successfully fabricated functional piezoceramics which have controllable curved shapes.
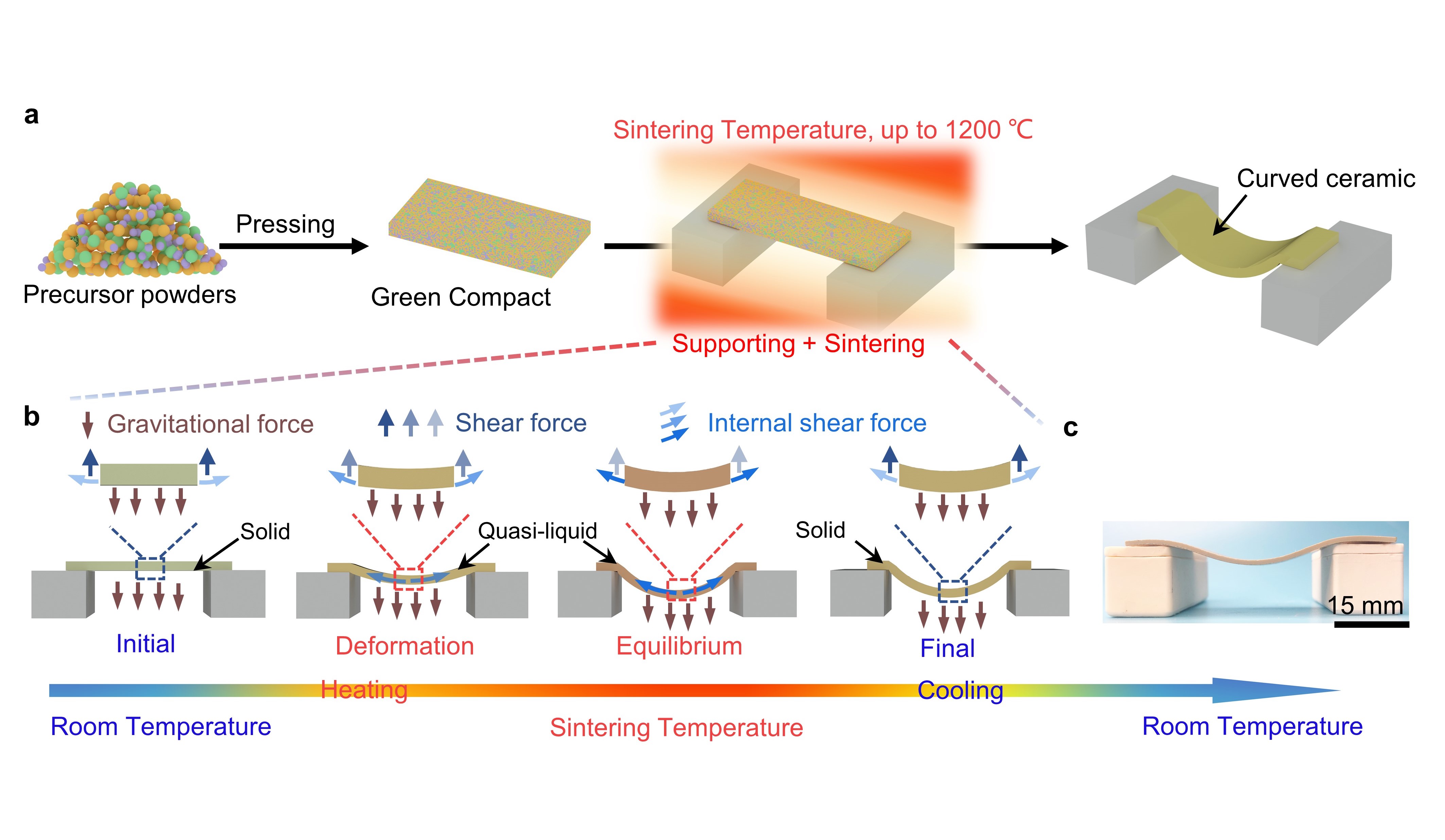
Credit: Shan, Y., Liu, S., Wang, B. et al. / DOI number: 10.1038/s41467-021-26373-x
“Our sintering method’s principle is simple. By adjusting the position of the supporting objects beneath the piezoceramics, we can tune its curvature. Most importantly, our method would not affect the high piezoelectric performance of the material,” said Dr Yang.
The research team proposed a pioneering piezoceramics fabrication method called the gravity-driven sintering (GDS) technique that shapes piezoceramics during the sintering process. The team first pressed the piezoceramics material into a compact, then put supporting objects beneath it depending on the curve needed. After that, both the compact and the supporting objects would be put inside the furnace and sintered at a high temperature of up to 1,200 °C.
“During the sintering process, the solid compact would be softened because of the high temperature. Then the compact hang between two supporting objects would start sagging due to gravity, which created the curve. The curved compact would later be cooled down and keep its curved form,” explained Professor Lim Chee Wah, Professor in CityU’s Department of Architecture and Civil Engineering. He is one of the research team members.
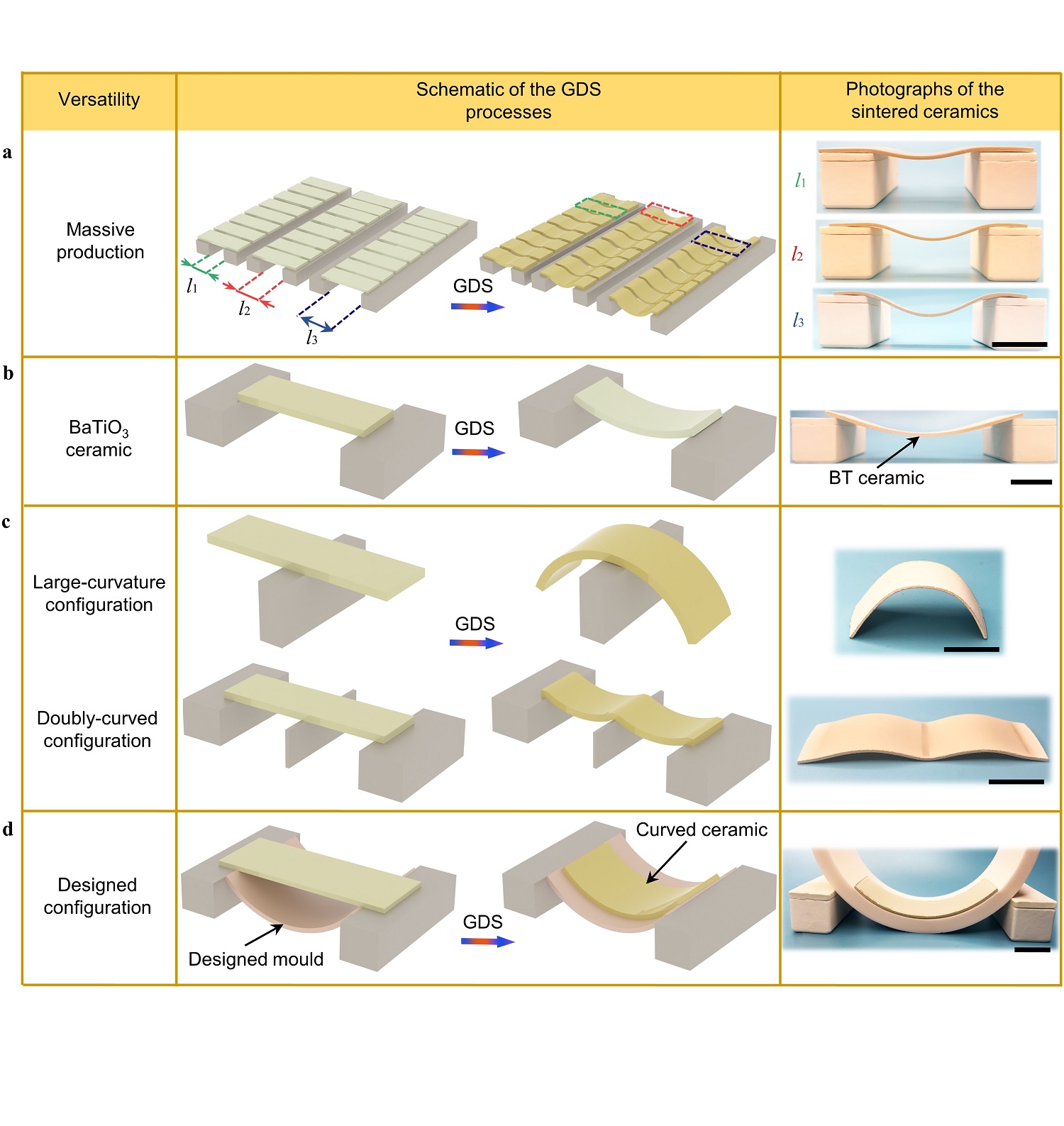
Credit: Shan, Y., Liu, S., Wang, B. et al. / DOI number: 10.1038/s41467-021-26373-x
Changing the supporting position to tune the curvature
The team tuned the curvature of the fabricated piezoceramics by changing the supporting position beneath it before the sintering process. The farther the supporting position were apart, the larger the curve would become in the fabricated piezoceramics. If the supporting position is right beneath the middle of the piezoceramics compact, then both the right and left sides would sag because of gravity during sintering, as a result, piezoceramics in arched shape would be made. If a designed mould is put beneath, then the piezoceramics would have a curve that is shaped by the mould.
The team used aluminium oxide blocks that were bought from the market as the supporting objects. The reason for choosing aluminium oxide is that such material is heat-resistant with good thermal conductivity, and does not react with the piezoceramics. The team applied the GDS method and fabricated lead zirconate titanate (PZT) piezoceramics in three different shapes.
Experiment results showed that these fabricated piezoceramics were of high compactness, and exhibited comparable high piezoelectric and mechanical properties with conventional-sintered samples. “We are the first team to achieve controllable shaping in sintering piezoceramics without sacrificing mechanical and piezoelectric properties,” added Dr Yang.
Shaping without sacrificing material properties
The fabricating method is simple, involves low cost and does not require delicate equipment, allowing great flexibility for users to design piezoceramics in different shapes. It is also applicable to other functional ceramics, and easy to scale up in production.
“The GDS method we developed can make piezoceramics components with different shapes. We see this work as a step towards producing functional ceramic-based devices that simultaneously possess geometrical complexity and good functionalities. And we believe that this new method will greatly accelerate the development of functional ceramic-based devices and expand their real-world applications, such as producing sensors and actuators of high efficiency,” concluded Dr Yang.
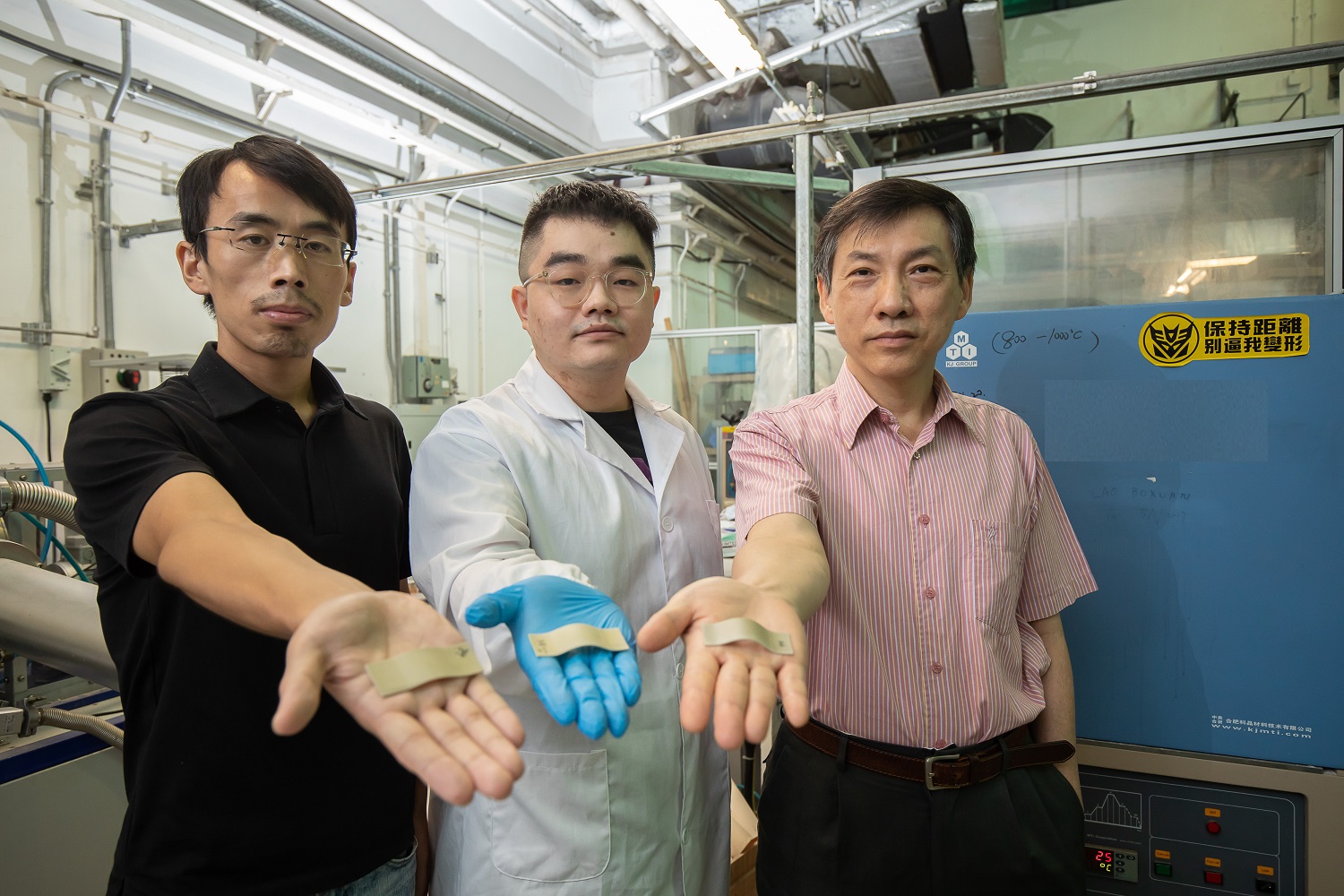
Credit: City University of Hong Kong
Dr Yang is the paper’s corresponding author. The first author is Shan Yao, a PhD candidate from MNE, CityU. Apart from Professor Lim, Liu Shiyuan , Wang Biao, and Hong Ying, PhD candidates from MNE, also participated in the research. Other collaborators are from Huazhong University of Science and Technology, including Professor Zhang Guangzu.
The research was supported by the Research Grants Council of Hong Kong and the Shenzhen Fundamental Research Program.
DOI number: 10.1038/s41467-021-26373-x