Discovery of grain-boundary disordered nanolayers in intermetallic alloys
Intermetallic alloys potentially have high strength in a high-temperature environment. But they generally suffer poor ductility at ambient and low temperatures, hence limiting their applications in aerospace and other engineering fields. Yet, a research team led by scientists of City University of Hong Kong (CityU) has recently discovered the disordered nanoscale layers at grain boundaries in the ordered intermetallic alloys. The nanolayers can not only resolve the irreconcilable conflict between strength and ductility effectively, but also maintain the alloy’s strength with excellent thermal stability at high temperatures. Designing similar nanolayers may open a pathway for the design of new structural materials with optimal alloy properties.
This research was led by Professor Liu Chain-tsuan, CityU’s University Distinguished Professor and Senior Fellow of the Hong Kong Institute for Advanced Study (HKIAS). The findings were just published in the prestigious scientific journal Science, titled “Ultrahigh-strength and ductile superlattice alloys with nanoscale disordered interfaces”.
Just like metals, the inner structure of intermetallic alloys is made of individual crystalline areas knows as “grains”. The usual brittleness in intermetallic alloys is generally ascribed to the cracking along their grain boundaries during tensile deformation. Adding the element boron to the intermetallic alloys has been one of the traditional approaches to overcome the brittleness. Professor Liu was actually one of those who studied this approach 30 years ago. At that time, he found that the addition of boron to binary intermetallic alloys (constituting two elements, like Ni3Al) enhances the grain boundary cohesion, hence improving their overall ductility.
A surprising experimental result
In recent years, Professor Liu has achieved many great advances in developing bulk intermetallic alloys (intermetallic alloy is also called superlattice alloy, constructed with long-range, atomically close-packed ordered structure). These materials with good strengths are highly attractive for high-temperature structural applications, but generally suffer from serious brittleness at ambient temperatures, as well as rapid grain coarsening (i.e. growth in grain size) and softening at high temperatures. So this time, Professor Liu and his team have developed the novel “interfacial nanoscale disordering” strategy in multi-element intermetallic alloys, which enables the high strength, large ductility at room temperature and also excellent thermal stability at elevated temperatures.
“What we originally tried to do is to enhance the grain boundary cohesion through optimizing the amount of boron,” said Dr Yang Tao, a postdoc research fellow at CityU’s Department of Mechanical Engineering (MNE) and IAS, who is also one of the co-first authors of the paper. “We expected that, as we increased the amount of boron, the alloy would retain ultrahigh strength due to its multi-element constituents.”
According to conventional wisdom, adding trace amounts (0.1 to 0.5 atomic percent (at. %)) of boron substantiallyimproves their tensile ductility by increasing grain-boundary cohesion. When excessive amounts of boron were added, this traditional approach would not work. “But when we added excessive amounts of boron to the present multicomponent intermetallic alloys, we obtained completely different results. At one point I wondered whether something went wrong during the experiments,” Dr Yang recalled.
Resolving alloys’ strength-ductility trade-off and thermal instability
To the team’s surprise, when increasing boron to as high as 1.5 to 2.5 at. %, these boron-doped alloys became very strong but very ductile. Experiment results revealed that the intermetallic alloys with 2.5 at. % of boron have an ultrahigh yield strength of 1.6 gigapascals with tensile ductility of 25% at ambient temperatures.
By studying through different transmission electron microscopies, the team discovered that when the concentration of boron ranged from 1.5 to 2.5 at. %, a distinctive nanolayer was formed between adjacent ordered grains. Each of the grains was capsulated within this ultrathin nanolayer of about 5 nm thick. And the nanolayer itself has a disordered atomic structure. “This special phenomenon had never been discovered and reported before,” said Professor Liu.
Their tensile tests showed that the nanolayer serves as a buffer zone between adjacent grains, which enables plastic-deformation at grain boundaries, resulting in the large tensile ductility at an ultrahigh yield strength level.
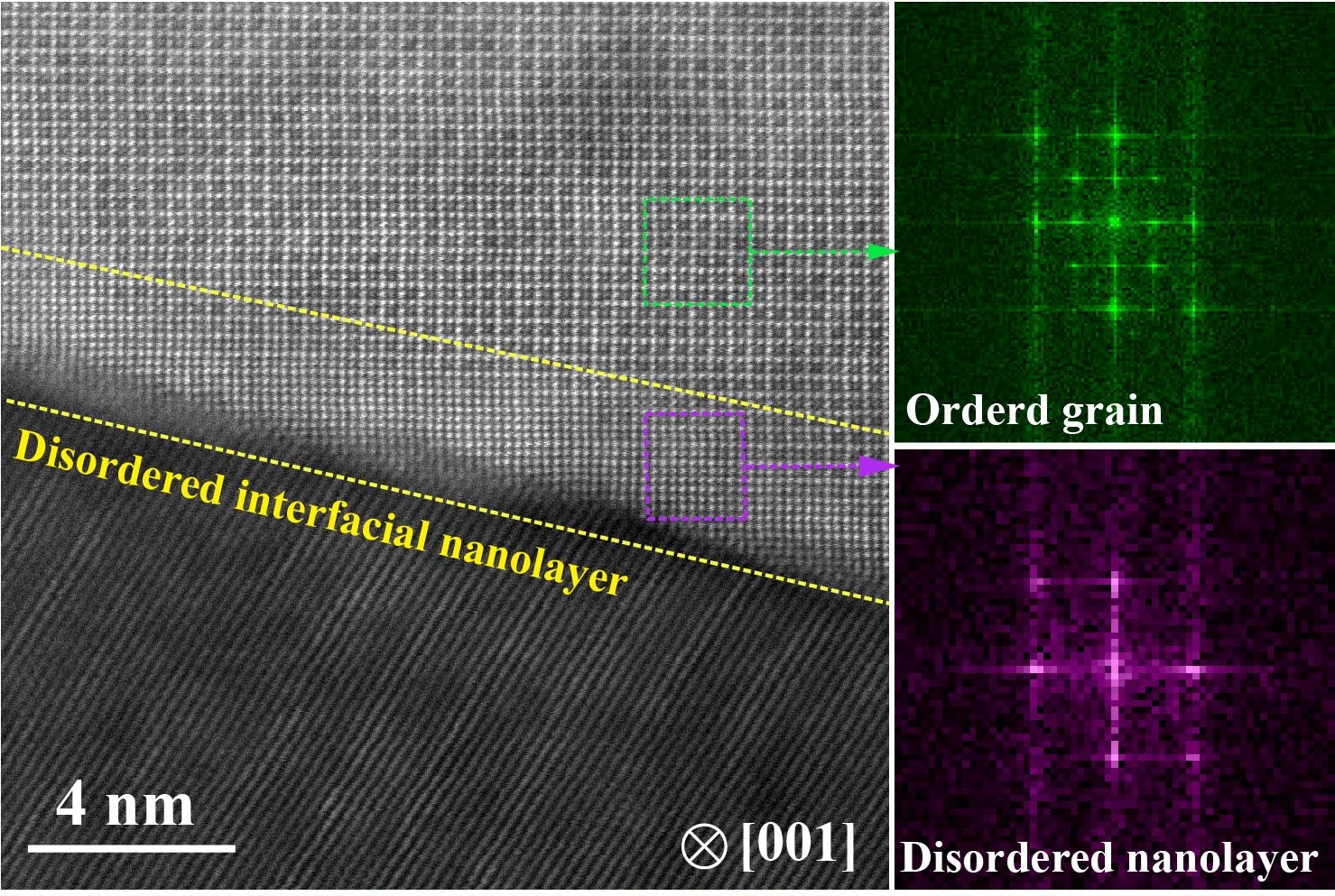
Why is the disordered nanolayer formed?
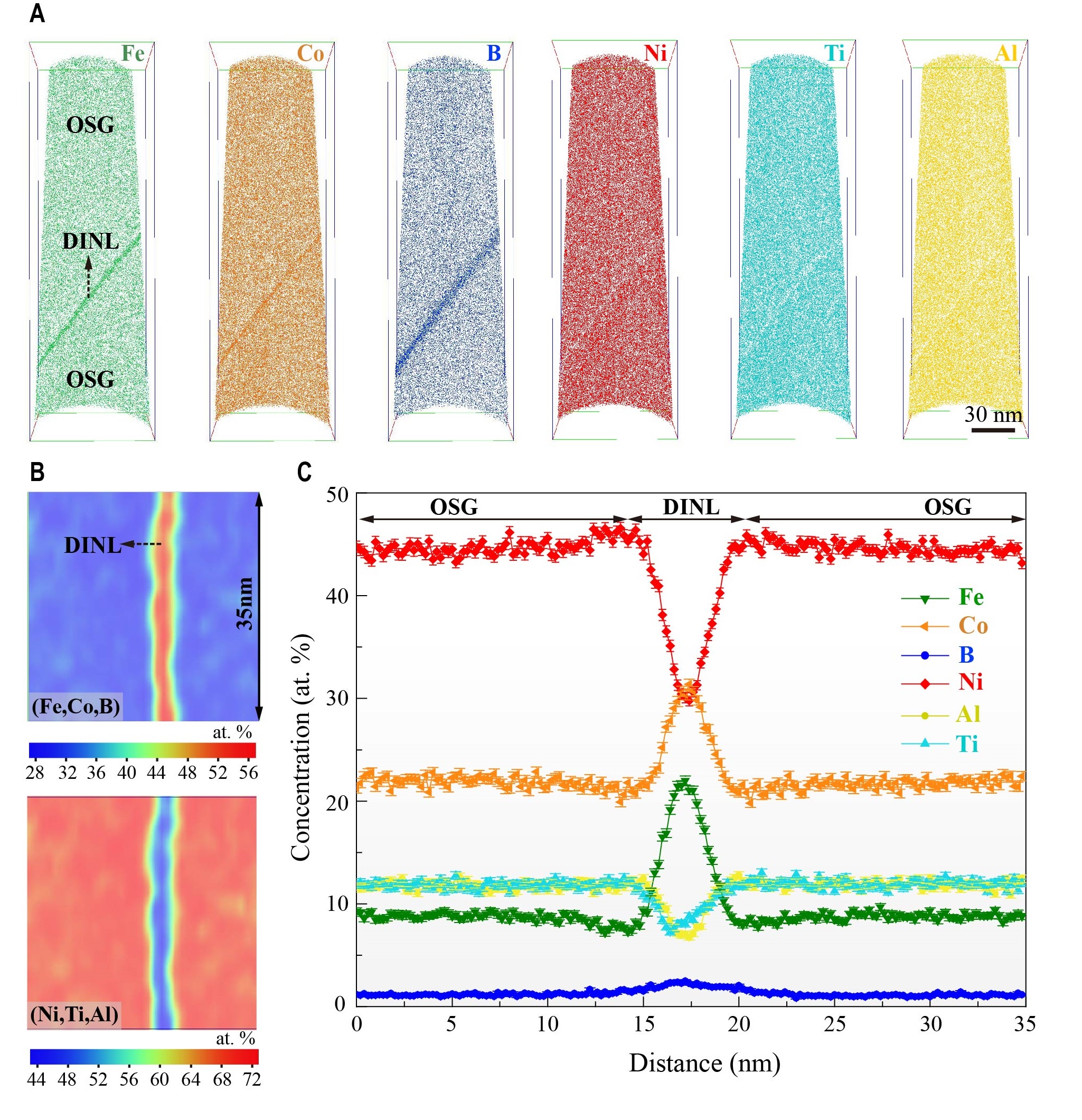
The team found that the further increase in boron has substantially enhanced the “multi-element co-segregation” – the partitioning of multiple elements along the grain boundaries. With the advanced three-dimension atom probe tomography (3D APT) at CityU, the only one of its kind in Hong Kong and southern China, they observed a high concentration of boron, iron, and cobalt atoms within the nanolayers. In contrast, the nickel, aluminium, and titanium were largely depleted there. This unique elemental partitioning, as a result, induced the nanoscale disordering within the nanolayer which effectively suppresses the fractures along grain boundaries and enhances the ductility.
Moreover, when evaluating the thermal response of the alloy, the team found that the increase in grain size was negligible even after 120 hours of annealing at a high temperature of 1050°C. This surprised the team again because most of the structural materials usually show the rapid growth of grain size at high temperatures, resulting in strength decrease quickly.
A new pathway for developing structure materials for high-temperature uses
They believed that the nanolayer is pivotal in suppressing growth in grain size and maintain its strength at high temperatures. And the thermal stability of the disordered nanolayer will render this type of alloy suitable for high-temperature structural applications.
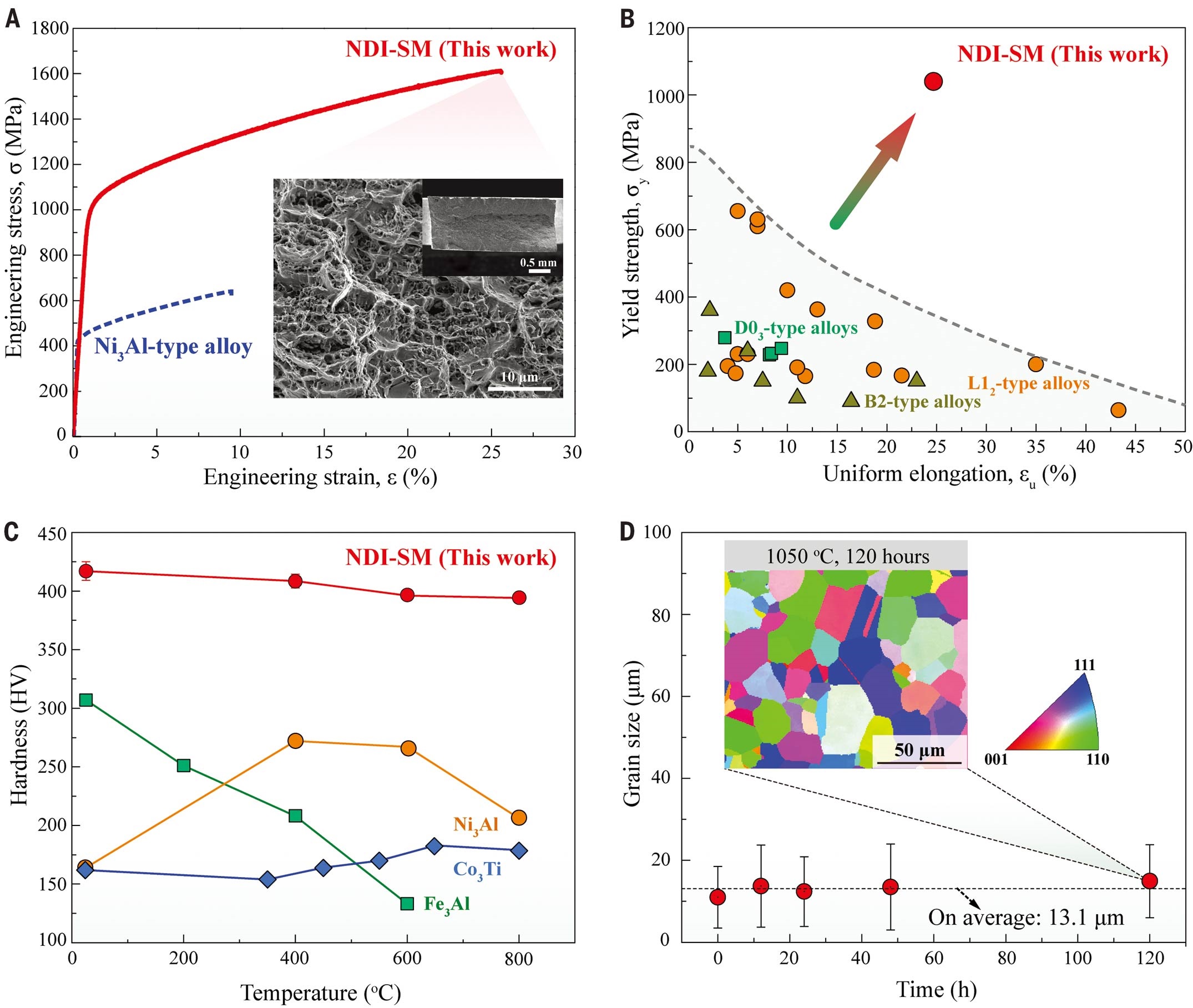
“The discovery of this disordered nanolayer in the alloy will be impactful to the development of high-strength materials in the future. In particular, this approach can be applied to structural materials for applications at high-temperature settings like aerospace, automotive, nuclear power, and chemical engineering,” said Professor Liu.
Professor Liu is the corresponding author of the paper. The co-first authors are Dr Yang Tao and Dr Zhao Yilu from MNE department at CityU. Other co-authors from CityU included: Professor Huang Chih-ching, Chair Professor of Materials Science and Executive Director of HKIAS, Professor Kai Jijung, Chair Professor of Nuclear Engineering, Li Wanpeng from Department of Materials Science and Engineering, and Dr Luan Junhua at the Inter-University 3D APT Unit.
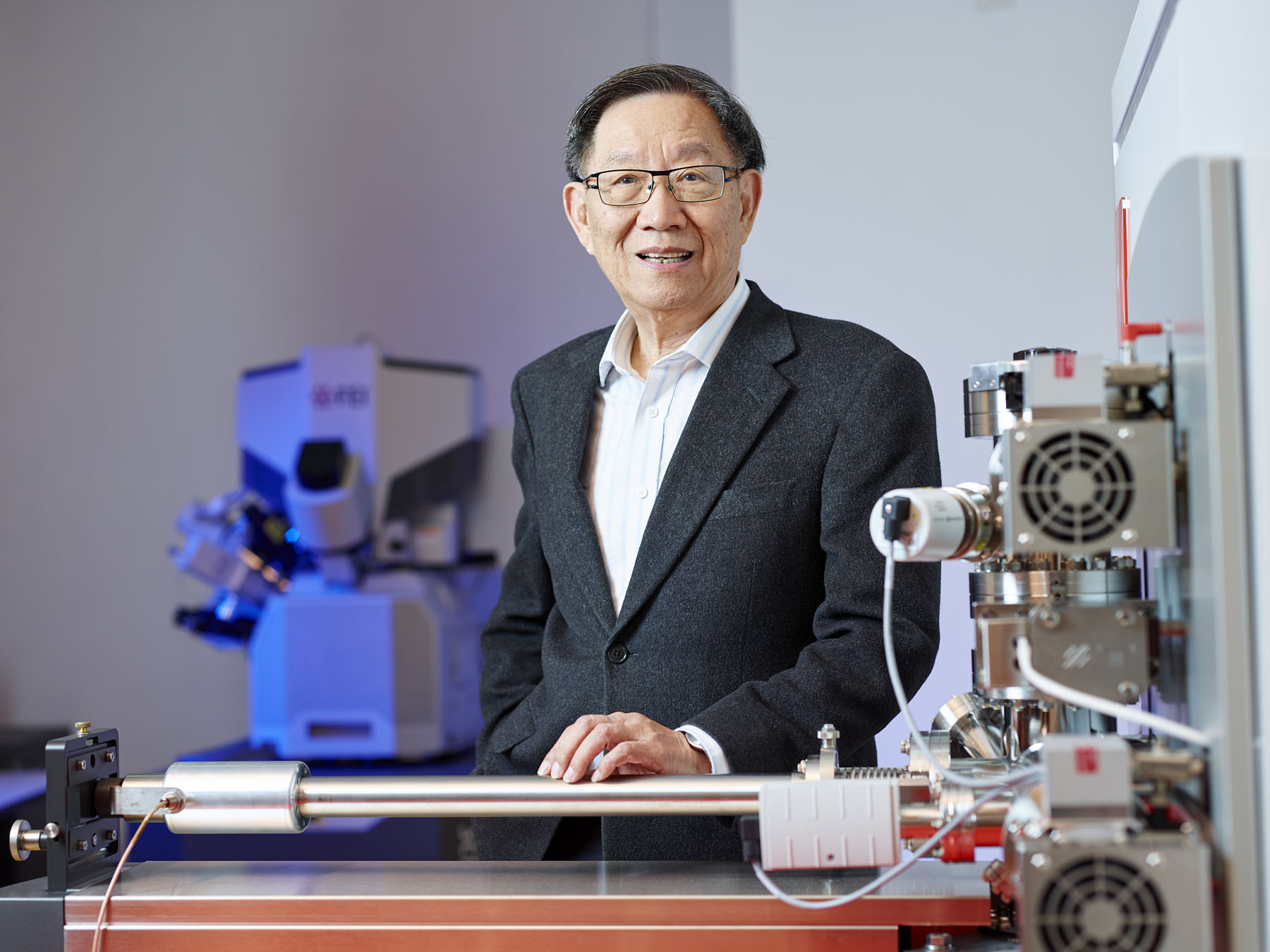
The funding support of the study included CityU, the Hong Kong Research Grant Council, and the National Natural Science Foundation of China.
DOI number: 10.1126/science.abb6830