A new generation of nanostructured aluminium alloy with ultrahigh strength and large plasticity
High strength and high ductility are often mutually exclusive properties for structural metallic materials. A recent study led by the City University of Hong Kong (CityU) revealed a new strategy to overcome this trade-off dilemma. Aided by molecular dynamics simulations, the research team developed a hierarchical nanostructured aluminium alloy composed of amorphous-nanocrystalline structures. This new aluminium alloy achieves the highest strength and high ductility of its kind so far. It can be applied to micro-electromechanical systems (MEMS) for flexible wearable devices in the future.
Professor Lu Jian, CityU’s Vice President (Research and Technology) and Director of both the Hong Kong Branch of National Precious Metals Material Engineering Research Center as well as the Centre for Advanced Structure Materials, and the Chair Professor of the Department of Mechanical Engineering, led the research team. The team successfully developed the first-ever supra-nano-dual-phase magnesium alloy previously. That cutting-edge new material is 10 times stronger than conventional crystalline magnesium alloy and has super-deformation capacity two times higher than that of magnesium-based metallic glass. In addition, it can be developed into biodegradable materials that can be implanted in the human body. That major research breakthrough became the cover story of Nature, an international top academic journal, and published on May 4, 2017.
The team did not stop there and set their sights on the development of materials with both high strength and high ductility. Recently, they have successfully fabricated a “hierarchical nanostructured aluminium alloy” using advanced nanostructure control technology. The hierarchical nanostructured aluminium alloy was composed of face-centered-cubic (fcc) nanograins with a diameter of about 40 nanometres (nm) and surrounded by 4-nm-thick metallic glass shells.
In general, stronger crystalline alloys are usually designed by controlling defects to hinder dislocation (a crystal defect of locally irregular arrangement of atoms) motion. However, different strengthening approaches often decrease ductility as a compromise. Ductility is the ability of an object to be deformed when an external force is applied. When the external force exceeds a certain value, the object will have irreversible deformation, called plastic deformation. So how did this study by CityU harvest both fish (high strength) and bear's paw (high ductility) at the same time?
Combination of metallic glass and crystalline material
The key lies in combining nanometre-sized amorphous metallic glass with crystalline nanomaterials. Metallic glass, also known as amorphous metal, has different deformation mechanisms. In the absence of dislocation-mediated crystallographic slip, metallic glass shows a large elastic deformation of 2% prior to yielding and exhibits a higher yield strength than crystalline alloys.
On the other hand, plastic deformation of metallic glass at room temperature occurs mainly in nano-scale shear bands (inhomogeneous deformation region). This will soften the material and eventually lead to fracture. Therefore, if the shear banding of the metallic glass phase is to be fully suppressed, theoretically, the size of the metallic glass needs to be smaller than 100 nm (or even 10 nm). In this case, the material’s strength can be significantly improved while retaining its plastic deformation.
In this direction, the team have recently developed a hierarchical nanostructured aluminum alloy, with a structure of aluminium nanograins encapsulated by an extremely thin metal glass shell. This structure allows the material harvest both the plastic flow of the nano-sized metallic glass phase and the strain hardening (meaning the hardness increase during straining) of the crystalline phase.
![The top middle picture is the optical image of the hierarchical nanostructured aluminium alloy. Fig f is the high resolution transmission electron microscope (HRTEM) image of the alloy, showing a crystalline aluminium nanograin surrounded by amorphous phase (post-colored by light yellow). The white dashed rectangle region in fig f shows the fcc structure with zone axis of [0 1 1]. (Photo source: Nat Commun 10, 5099 (2019) doi:10.1038/s41467-019-13087-4)](/sites/g/files/asqsls3821/files/inline-images/optical%20image-resized.jpg)
(Photo source: Nat Commun 10, 5099 (2019) doi:10.1038/s41467-019-13087-4)
High in strength and large in ductility
Experimental data showed that the hierarchical nanostructured aluminium alloy has an ultrahigh compressive yield strength of 1.7 GPa and a tensile yield strength of 1.2 GPa. In contrast, aluminium-based metallic glass has a compressive yield strength of only 1.0 GPa without any plasticity, while nanocrystalline aluminium has a compressive yield strength of only 0.2 GPa. The research team believes that the nano-scale metallic glass in the hierarchical nanostructured aluminum alloy is close to the ideal strength due to its extremely small size.
Moreover, the nano-scale metallic glass phase replaces the grain boundaries, therefore effectively impedes grain boundary migration, which prevents softening mechanisms from taking place. Nano-scale metallic glass also blocks dislocations move from one grain to another, contributing to the alloy’s ultrahigh strength.
During plastic deformation, the encapsulating metallic glass phase exhibits flow behaviour due to its small size. Dislocations are initiated from the nanograin / metallic glass interfaces. Some dislocations pile up in the nanograins and provide strain hardening, while the majority of the dislocations move within the nanograins and are annihilated at another nanograin / metallic glass interface (absorbed by the atoms at the boundary). This kind of dislocation is called the transitory-dislocations. The continuous generation-movement-annihilation of transitory-dislocations in the nanograins and the intrinsic plastic flow of the nano-sized metallic glass phase contribute to the aluminium alloy’s large plasticity. Experimental data shows that the hierarchical nanostructured aluminium alloy exhibited a large plastic deformation with a strain of over 70%.
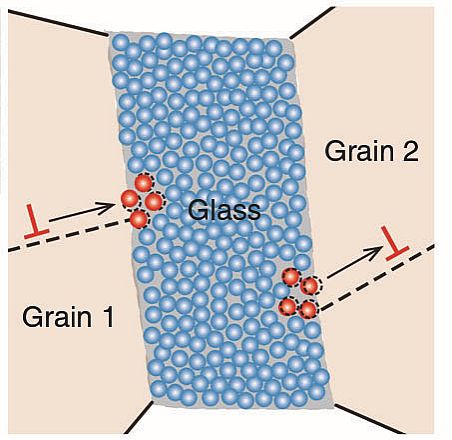
(photo source: Nat Commun 10, 5099 (2019) doi:10.1038/s41467-019-13087-4)
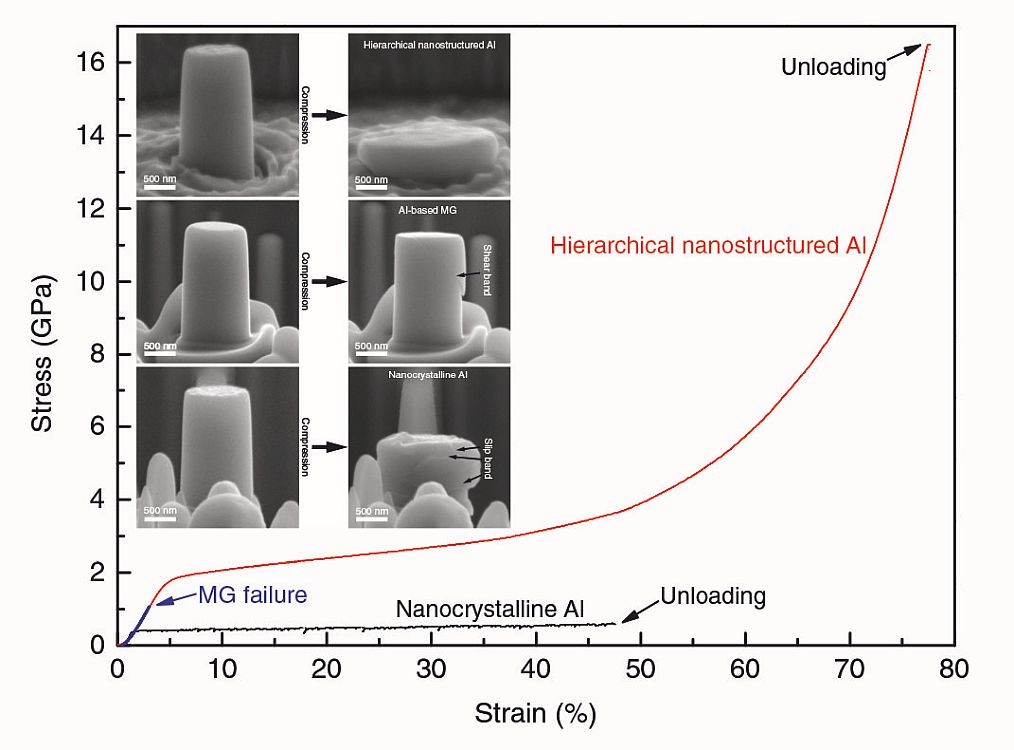
(photo source: Nat Commun 10, 5099 (2019) doi:10.1038/s41467-019-13087-4)
The research data also shows that under compression, the hierarchical nanostructured aluminium alloy displayed homogeneous deformation. The vertical width of the nanograins decreased from ~40 to ~ 8 nm after compression, while the width of the metallic glass phase decreases from ~4 to ~1 nm without any shear bands. The result confirms the team's hypothesis about suppressing the formation of shear bands.
Extensive application of aluminium alloy
"This research achievement successfully demonstrates a new hierarchical nanostructure approach in material engineering," said Professor Lu. "This method of developing aluminium alloy can contribute to the development of tough, lightweight alloys for the applications of microelectromechanical systems (MEMS) in flexible wearable devices."
Their research findings were published in the scientific journal Nature Communications, titled “Hierarchical nanostructured aluminum alloy with ultrahigh strength and large plasticity”. Professor Lu is the corresponding author of the paper. The first, second, and third authors are all from CityU. They are Dr Wu Ge, Dr Liu Chang (both currently postdoctoral researchers of Max-Planck-Institut für Eisenforschung) as well as Dr Sun Ligang (currently an Assistant Professor at Harbin Institute of Technology). Research team members from CityU also included Professor Liu Chain Tsuan, Senior Fellow of CityU’s Hong Kong Institute for Advanced Study and University Distinguished Professor at CityU, Professor Kai Ji-jung and Dr Lu Yang from Department of Mechanical Engineering, Dr Wang Qing (currently a professor at Shanghai University), Dr Han Bin (currently an Associate Professor at Shaanxi University of Science & Technology), Senior Research Associate Dr Luan Junhua, Research Associate Cao Ke and PhD student Cheng Lizi.
The research was supported by CityU, Research Grants Council of Hong Kong, the National Key R&D Program of China, and the Major Program of the National Natural Science Foundation of China.
DOI number: 10.1038/s41467-019-13087-4
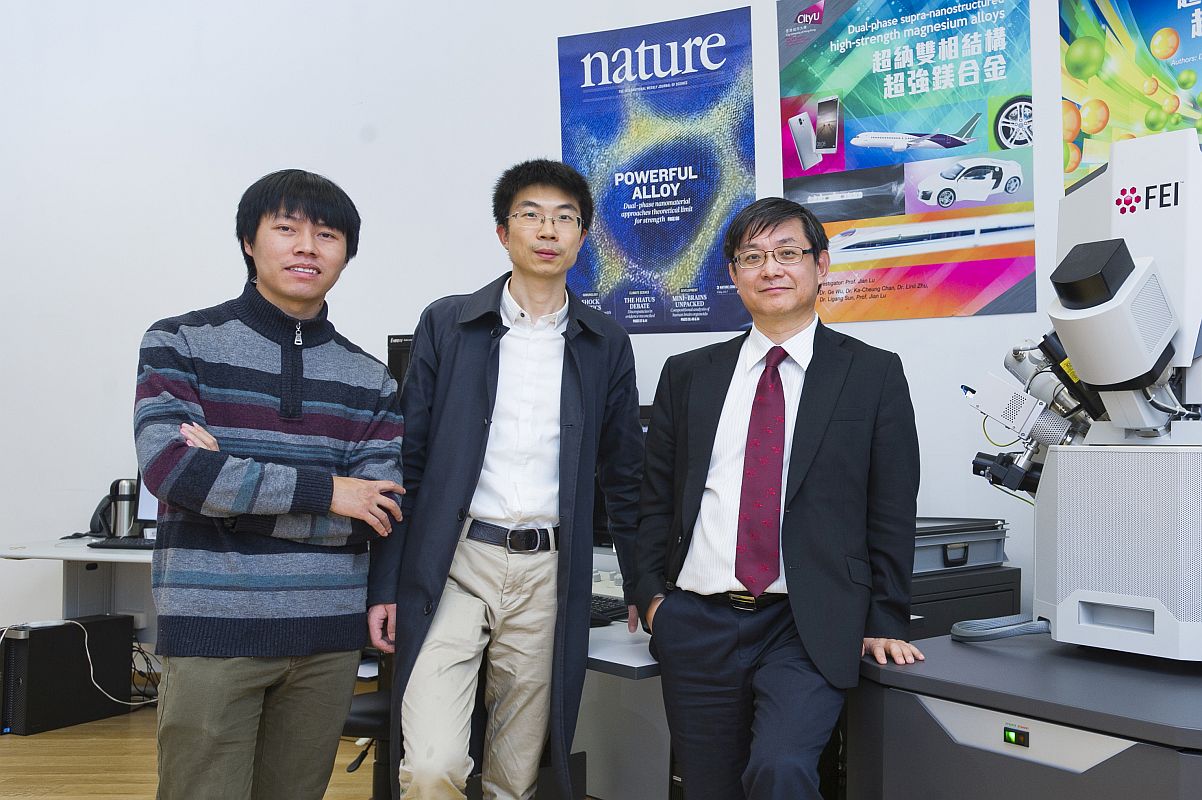